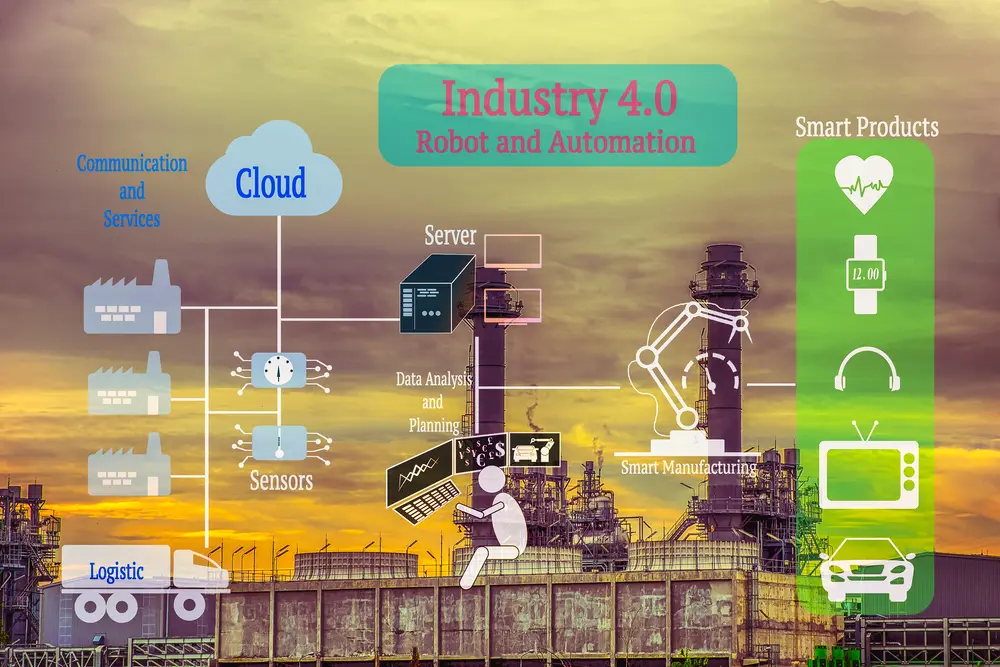
Nei prossimi anni, la 4à rivoluzione industriale garantirà ricavi aggiuntivi per 500 miliardi di dollari e minor costi per 421 miliardi, anche grazie ai software per il controllo della produzione industriale. Secondo alcuni esperti, però, l’Italia sarebbe in ritardo in questo percorso che non solo vuole connettere le fabbriche ma anche integrare cultura digitale e nuove competenze. L’industria 4.0 è sempre più al centro delle agende dei manager ma, nonostante gli sforzi, rischia di rimanere uno slogan, con buona pace di tutti i benefici potenziali in termini di efficienza e produttività. L’ingresso nella quarta rivoluzione industriale rappresenta ancora una chimera per molte imprese, frenate dall’assenza di cultura dell’innovazione, vision operativa e leadership digitale dei manager e confuse circa l’effettivo ritorno sugli investimenti digitali. Anche se i prossimi anni potrebbero riservare sorprese positive. Questi elementi emergono dal rapporto globale sull’industry 4.0, condotto in 26 Paesi sparsi nel mondo. Il passaggio dal paradigma 3.0, ossia di quello che ha spinto l’automazione di un singola macchina o di un singolo processo, alla sua evoluzione, che riguarda la digitalizzazione end-to-end di tutta l’azienda, dagli asset fisici alla catena del valore che coinvolge i partner, non è una sfida da poco. Ma i benefici sono enormi, come dimostra la stima effettuata sui business di coloro che già ci stanno investendo e che ci investiranno nei prossimi anni.
Secondo i calcoli l’industria 4.0 garantirà da qui al 2020 493 miliardi di dollari di ricavi aggiuntivi e consentirà di ridurre i costi per 421 miliardi, anche grazie ai software per il controllo della produzione industriale di GP Progetti, azienda bresciana che ha cominciato a pensare alla 4à rivoluzione industriale in tempi non sospetti, cioè 25 anni fa.
Scendendo nel dettaglio dal rapporto, è interessante notare che in termini assoluti il rapporto tra investimenti e risparmi alla voce di spesa non restituisce lo stesso indice in tutti i settori. Ad esempio, l’elettronica è il mercato che investirà di più, oltre 230 miliardi, ottenendo un risparmio sui costi di 62 miliardi. Mentre il settore dei trasporti e della logistica risparmierà circa 60 miliardi di spesa a fronte di 97 miliardi investiti. Segno di una quarta rivoluzione industriale dagli effetti diversificati e da valutare con attenzione. In ogni caso, il doppio binario di ricavi aggiuntivi e riduzione dei costi sarà spinto, da un lato, dall’innovazione di prodotto e servizio in un’ottica sempre più nativamente digitale, e dall’altro, dalla riduzione dei tempi operativi e dal miglior utilizzo degli asset che consentono di massimizzare la qualità del prodotto. Un circolo virtuoso su cui le aziende prevedono di investire nei prossimi 4 anni 907 miliardi di dollari, in media il 5% del proprio fatturato. Soldi destinati non solo a sensori, device connessi, software per il controllo della produzione industriale e applicazioni digitali. Ma anche al training dei dipendenti e alle modifiche della macchina organizzativa. La grande sfida, spiegano gli analisti, non è solo tecnologica. Riguarda invece il fattore umano, con il successo delle aziende 4.0 che dipende in gran parte da come ceo, cio e cto definiscono, guidano e comunicano la trasformazione digitale. Un simile processo funziona cioè solo se l’innovazione diventa la priorità della squadra di comando e, a cascata, di tutti i dipendenti. “La componente tecnica è essenziale, ma senza l’apertura culturale del top manager come dell’impiegato, tanto nel pubblico quanto nel privato, non ci può essere industry 4.0 – avverte Andrea Rangone, ceo di Digital360, gruppo specializzato nella trasformazione digitale di imprese e PA – Gli imprenditori hanno un’opportunità unica per accrescere competitività e produttività, ma è un treno già in corsa. Temporeggiare significa rimanere fermi mentre i competitor conquistano mercato ed efficienza”. Lo scenario italiano non è molto confortante anche se l’avvio del Piano Industria 4.0 elaborato dal Governo, tra iperammortamenti, progetti per la formazione delle competenze e la nascita di infrastrutture abilitanti, dovrebbe dare una forte spinta. L’ultimo rapporto di Federmeccanica, che prende in considerazione 11 tecnologie abilitanti (robotica, IoT, big data, cloud, stampa 3D e altre), rivela che il 36% delle nostre imprese non ne adotta nemmeno una. Per fortuna c’è il restante 64% che si è già mosso e che, rispetto alle aziende tecnologicamente spoglie, esporta di più (44% contro 33%), investe maggiormente in R&S e formazione e ritiene il trio qualità-innovazione-personalizzazione più rilevante della variabile prezzo. “Nel nostro Paese si è innescato un circolo virtuoso, ma non riusciamo a decollare. Serve un elettroshock a tutti i livelli, che aumenti la consapevolezza dell’importanza, anzi della necessità, di investire massicciamente sull’innovazione digitale – spiega Rangone – Un passo deciso in questa direzione può arrivare solo se imprese, politica, scuola e istituzioni uniscono le forze e viaggiano unite, perché il gap digitale è trasversale”. Tra le possibili azioni da adottare, sottolinea il report Federmeccanica, le imprese indicano come prioritaria l’informazione circa gli strumenti finanziari a supporto degli investimenti, l’aggiornamento e la sensibilizzazione degli imprenditori e lo sviluppo di una campagna di comunicazione che individui aziende campione e diffonda buone pratiche. “Siamo il Paese delle tante Pmi e dei pochi big. Per questo motivo non dobbiamo accontentarci di qualche best practice, ma agire in un’ottica di sistema Italia – conclude il ceo di Digital360 – L’industry 4.0 è una delle ultime chiamate per gettare le basi di una vera crescita economica”. Fonte: La Repubblica, 6 marzo 2017